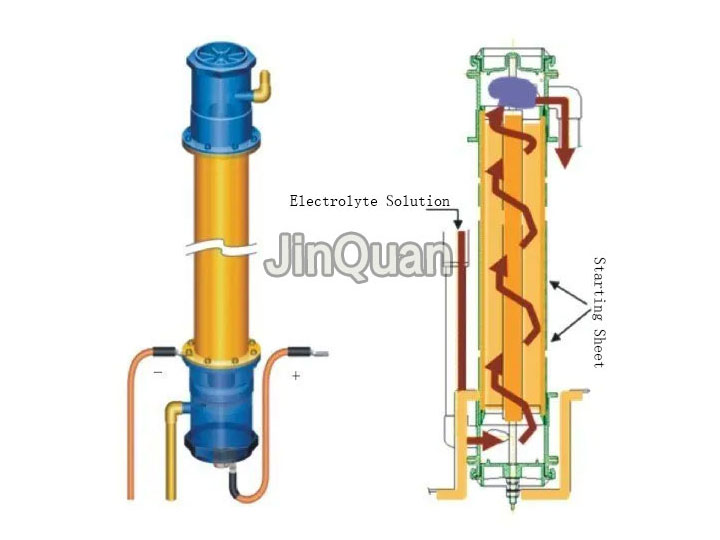
Rotating Electrode Technology and Conventional Electroplating Technology share the same electrochemical theoretical foundation. Both involve immersing the anode and cathode in an electrolyte solution containing target metal cations, achieving directed movement of ions under electric fields to deposit the target metal on the cathode.
The difference lies in that rotating electrode devices allow for higher flow velocity of the electrolyte solution, effectively utilizing the rapid flow of the electrolyte to eliminate concentration polarization phenomena during the electroplating process. This ensures more complete reaction and high purity of cathodic products with high current efficiency. It is particularly suitable for (wet metallurgical industry) in the selective electrolysis (electroplating) separation and purification of low-concentration and multi-component electrolyte solutions, or for removing metal ions from wastewater.
Applications:
1、Copper refining waste liquid purification;
2、Copper corrosion solutions copper recovery;
3、Zinc smelting slag copper and nickel recovery;
4、Copper, cobalt, nickel, zinc mixed metal ion solution copper, cobalt, nickel recovery;
5、Cyano solutions electrorefining Au and Ag recovery。
-
gold recovery from e wastegold recovery from e waste
Recycling Principle: The principle of recycling is based on electrochemistry, where gold ions dissolved in water are converted into metallic gold ions at the cathode, forming solid gold deposits.
Operation Method: A cyclic electroplating process is used. The water level in the tank is kept relatively low to minimize carryover to the next tank, aiming for higher recovery rates.
Recycling Efficiency: Achieves over 98% efficiency. In online cyclic recycling, levels can be maintained between 5-30 ppm, while offline single-recycling processes can reach as low as 0.5-10 ppm.
-
etching solution leachingetching solution leaching, electrolytic copper regeneration system
Etching Solution Leaching, Electrolytic Copper Regeneration System:
The copper leaching process generates a large amount of leaching waste, which contains copper ions (100-170 g/L), ammonia, and sodium chloride. Traditional handling methods involve selling the waste as is by PCB manufacturers, who use it as raw material to produce foam copper and other products via precipitation. However, this method fails to effectively utilize the excess ammonium ions and small amounts of copper ions, leading to resource wastage.
Our Innovative Process:We have adopted a solvent leaching - reverse leaching - electroplating process for the regeneration of leaching waste. This approach uses leaching to separate copper ions from the leaching waste without causing damage, achieving a clean separation. The leach solution is then separated into its components through fractionation. Once the leaching performance is restored, the entire solution is returned to the copper production line for reuse. Finally, we utilize electroplating technology to process the reverse-leached electrolyte, producing copper plates with over 99.5% purity.
-
colloid palladium adsorption recovery methodcolloid palladium adsorption recovery method
Colloid Palladium Adsorption Recovery Method:
Acidic colloid palladium is generated in the early activation treatment solution within the hole of the circuit board. Its composition consists of a sodium chloride bath and weak acid stabilization, as it has Sn encapsulation.
Reasons for Encapsulation with Tin:Due to the tin encapsulation, it's necessary to break through this layer to enable adsorption of palladium. Conventional resins or activated carbons are ineffective in this process, as they cannot easily penetrate or effectively adsorb palladium.
Our Custom-Built Activated Carbon:
To address this challenge, we have specifically developed and produced activated carbon optimized for the adsorption of acidic colloid palladium. This activated carbon achieves efficient recovery of colloid palladium, with an adsorption capacity ranging from 5 to 20 grams per liter.