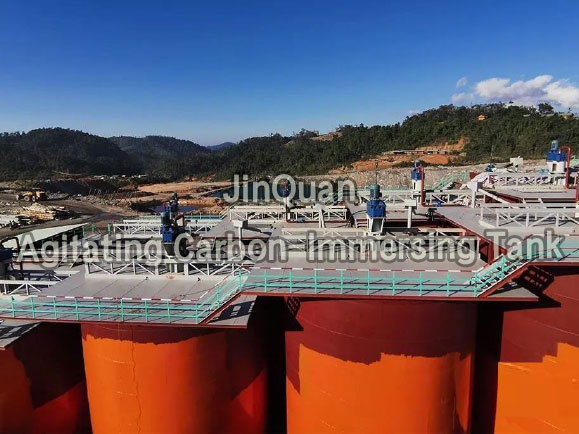
Features of Dual impeller high-efficient agitating carbon-immersing tank:
This product is used in carbon paste flow and cyanidation process. The carbon-immersing tank should match other auxiliary devices like carbon-separating screen, and recessed impeller pump, etc. Its structural features:the upper and lower layer of impellers are of steel plate encapsulated with rubber, which are connected by means of bolts, with the features like good equilibrium, easy replacement, and long service life. The main shats are divided into the upper layer and the lower layer, which areconnected by means of locating flanges, able to reduce the lifting height; inlate at several points dispersingly, with good air mixing performance.
Notes for Selection:
Planet cycloid reducing motor is usually adopted for driving, with the features like simple structure and low price. If gear wormdrive is required, please order it specially and specify it.
Technical parameter list of Dual impeller high-efficient agitating carbon-immersing tank
型号 Model | 槽体规格(mm) 直径 *高度 Size of the tank D*L | 有效容积 m3 Efective capacity | 叶轮转速 (r/min) Revolution of impeller | 叶轮直径 (mm) Diameter of impeller | 给矿管直径 (mm) Diameter of feeding pipe | 排矿管直径 (mm) Diamete of discharging pipe | 行星摆线减速器 | 重量 (kg) Weight | ||
型号Model | 速比 Speed ratio | 配用电机功率(kW) Motor power | ||||||||
⌀2 5 X 2 5 | 2500x2500 | 6 | 52 | 800 | 2- ⌀133 | 2- ⌀133 | XLD2 2-4-29 | 29 | 2.2 | 2800 |
⌀2 5 X 3 15 | 2500x 3150 | 13 | 52 | 935 | 2-⌀125 | 2- ⌀133 | XLD2 2-4-29 | 29 | 2.2 | 3120 |
⌀3 X 3.15 | 3000x 3150 | 18 93 | 43 | 1130 | 2-⌀150 | 2- ⌀150 | XLD4-5-35 | 35 | 4 | 5300 |
⌀7.5x8.0 | 7500x8000 | 268.6 | 21 | 2900 | 2-⌀159*8 | 2-⌀159*8 | XLD22-10-47 | 47 | 22 | 32796 |
⌀8.0x 8 5 | 8000 X 8500 | 342 | 16.4 | 3200 | 2-⌀159*8 | 2-⌀159*8 | XLD22-11-59 | 59 | 22 | 42467 |
-
gold recovery from e wastegold recovery from e waste
Recycling Principle: The principle of recycling is based on electrochemistry, where gold ions dissolved in water are converted into metallic gold ions at the cathode, forming solid gold deposits.
Operation Method: A cyclic electroplating process is used. The water level in the tank is kept relatively low to minimize carryover to the next tank, aiming for higher recovery rates.
Recycling Efficiency: Achieves over 98% efficiency. In online cyclic recycling, levels can be maintained between 5-30 ppm, while offline single-recycling processes can reach as low as 0.5-10 ppm.
-
etching solution leachingetching solution leaching, electrolytic copper regeneration system
Etching Solution Leaching, Electrolytic Copper Regeneration System:
The copper leaching process generates a large amount of leaching waste, which contains copper ions (100-170 g/L), ammonia, and sodium chloride. Traditional handling methods involve selling the waste as is by PCB manufacturers, who use it as raw material to produce foam copper and other products via precipitation. However, this method fails to effectively utilize the excess ammonium ions and small amounts of copper ions, leading to resource wastage.
Our Innovative Process:We have adopted a solvent leaching - reverse leaching - electroplating process for the regeneration of leaching waste. This approach uses leaching to separate copper ions from the leaching waste without causing damage, achieving a clean separation. The leach solution is then separated into its components through fractionation. Once the leaching performance is restored, the entire solution is returned to the copper production line for reuse. Finally, we utilize electroplating technology to process the reverse-leached electrolyte, producing copper plates with over 99.5% purity.
-
colloid palladium adsorption recovery methodcolloid palladium adsorption recovery method
Colloid Palladium Adsorption Recovery Method:
Acidic colloid palladium is generated in the early activation treatment solution within the hole of the circuit board. Its composition consists of a sodium chloride bath and weak acid stabilization, as it has Sn encapsulation.
Reasons for Encapsulation with Tin:Due to the tin encapsulation, it's necessary to break through this layer to enable adsorption of palladium. Conventional resins or activated carbons are ineffective in this process, as they cannot easily penetrate or effectively adsorb palladium.
Our Custom-Built Activated Carbon:
To address this challenge, we have specifically developed and produced activated carbon optimized for the adsorption of acidic colloid palladium. This activated carbon achieves efficient recovery of colloid palladium, with an adsorption capacity ranging from 5 to 20 grams per liter.