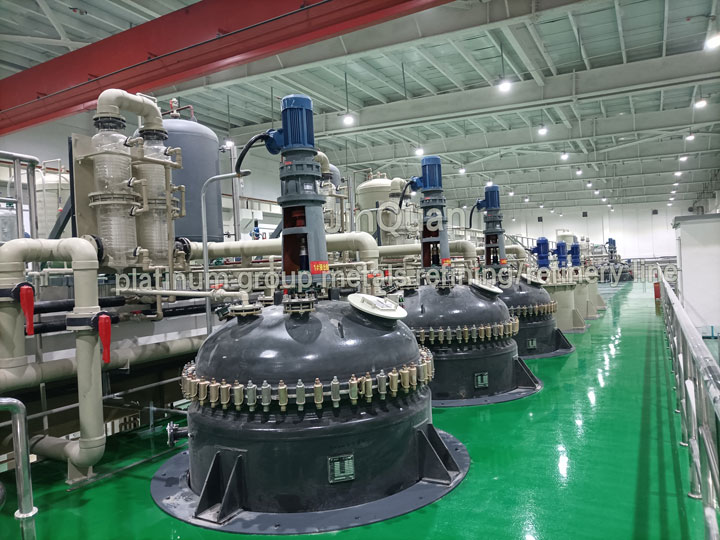
platinum group metals refining/refinery line Introduction:
Given the scarcity of domestic platinum group minerals and supply-demand imbalances, China depends mainly on imported resources to meet its needs. However, in recent years, a significant portion of domestically available platinum group metals comes from the recycling of industrial waste materials, such as platinum catalysts used in the petrochemical industry and catalytic converters from car exhaust systems. Different raw materials require different processing technologies and equipment. Based on the characteristics of each raw material, our company designs tailored processes and equipment to meet production requirements.
In September 2021, a collaborative project between our company and Northeast Normal University, titled "Short Process Cleaning and Efficient Separation and Refining Technology and Equipment for Platinum Group Metals," received recognition from Professors He Jieqiong and Huang Xiaowei. This project has been acknowledged by the Non-ferrous Metals Industrial Association of China as being on par with international advanced levels.
-
colloid palladium adsorption recovery methodcolloid palladium adsorption recovery method
Colloid Palladium Adsorption Recovery Method:
Acidic colloid palladium is generated in the early activation treatment solution within the hole of the circuit board. Its composition consists of a sodium chloride bath and weak acid stabilization, as it has Sn encapsulation.
Reasons for Encapsulation with Tin:Due to the tin encapsulation, it's necessary to break through this layer to enable adsorption of palladium. Conventional resins or activated carbons are ineffective in this process, as they cannot easily penetrate or effectively adsorb palladium.
Our Custom-Built Activated Carbon:
To address this challenge, we have specifically developed and produced activated carbon optimized for the adsorption of acidic colloid palladium. This activated carbon achieves efficient recovery of colloid palladium, with an adsorption capacity ranging from 5 to 20 grams per liter.
-
silver recovery process from fixing solutionsilver recovery process from fixing solution
Silver Recovery Process from fixing solution:
1、After the silver electrolysis recovery device is installed, it waits for the output of mercury from the fiinling machine to enter the storage tank of the recovery device.
2、When the water level in the storage tank reaches the preset level, it automatically starts the water pump to begin electrolysis.
3、Upon completion of the electrolysis process, the waste from the process is automatically discharged.
4、Once the water level in the storage tank reaches the preset level again, it draws water from the storage tank to the electrolysis tank.
5、If the water level in the storage tank does not reach the preset level, it waits for the fiinling machine to output water into the storage tank. At this time, the recovery device is in a stopped state until it reaches the preset level again and restarts.
6、After the silver-containing fiinling solution undergoes electrolysis, the concentration of silver ions is below 2-10 ppm. After using specialized silver recovery resin for absorption, the silver ion concentration drops below 0.1 ppm, meeting the environmental standards for discharge as set by Table Three.
-
Innovative Gold and Silver Recovery Extraction TechnologyInnovative Gold and Silver Recovery Extraction Technology
Innovative Gold and Silver Recovery Extraction Technology
Device Utilizes Advanced Electrolysis Methods: Employs rotating cathode, high-frequency pulse technology for intelligent electrorefining without any chemical reagents or consumables, utilizing minimal electricity (350W), with no secondary pollution affecting subsequent treatment of the solution.
Compact Design and User-Friendly Operation: Small, space-saving design allows easy operation without dedicated personnel; incorporates anti-corrosive design to extend component lifespan and handle large processing volumes.
Low Metal Content in Post-Electrolysis Waste: Post-process waste contains less than 2-10 ppm of metal content.
No Special Tools Required for Silver Recovery: Silver content in recovered dross is typically 96-98%, allowing direct refining to produce silver ingots exceeding 99% purity through simple melting.
Single Purification Step for Gold: Requires a single purification step due to gold's small size and tendency to shed, minimizing unnecessary waste.
Series Production and Customization Available: The product is ready for mass production with complete specifications, also offering customization options based on client requirements.